PREVENTION IS THE BEST CURE – Surface Discoloration of a New Concrete Floor
Exposed Concrete
Exposed concrete floor surfaces have become increasingly popular over the last two decades. The number of decorative finishes to exposed concrete has helped boost this trend. There is a tremendous variety of colors, patterns and finishes to the concrete flatwork.
The expectation of quality of a decorative concrete floor has risen as well. Daniel Green, a retired Technical Service Manager, states in his article “Discolored Concrete Flatwork”: that the “Standards for the surface appearance of flatwork have risen considerably. The non-uniform color of concrete slab surfaces can be a point of cosmetic issue, often to the point of owner rejection. The expectation is for the concrete to be attractive in color/shading uniformity.”1 What are the potential problems, causes, and means of reducing the risk of differences of color and shading on your new concrete floor?
What causes concrete discoloration?
There are a wide variety of causes for the discoloration of a concrete flatwork’s surface. As is often the case, knowledge and early planning can reduce the risk of this situation. In this article, we’ll discuss the most common causes for the surface to vary in color and shading and what can be done to prevent it.
The Portland Cement Association lists several primary factors that can cause the discolorations:
- Calcium chloride additions
- Hard troweled surfaces
- Inadequate, inappropriate, and/or lack of curing
- Variations of the water cement ratio at the surface
- Changes (of raw materials) in the concrete mix2
Additionally, there is another dimension to the problem. It is that there can be a lot of variations in what occurs on the surface of the concrete. The discoloration of the concrete surface can be gross changes over large areas of concrete, blotches over some areas, or smaller spotty or mottled areas on the surface. Let’s take a look at the mechanism that causes each of these problems and what should be done to reduce the risk.
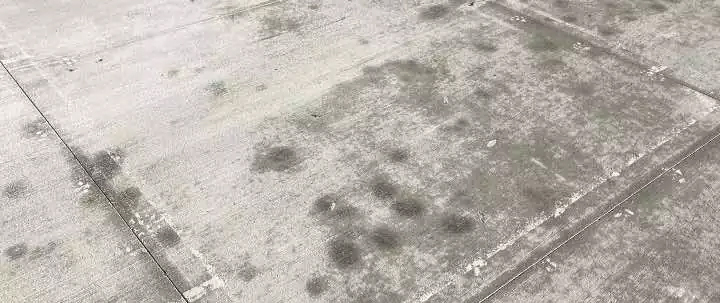
Calcium chloride additions
Calcium chloride is often used as an accelerant in a concrete slab. It helps to increase the speed of the chemical reaction (hydration) that occurs in the concrete mixture. This is particularly important in cold weather where the cold temperatures tend to slow the reaction. The calcium chloride improves the reaction rate which helps in the placement and finishing of the concrete.
The advantages of using calcium chloride are obvious. On the other hand, if the amount of calcium chloride used in the concrete mix is too high, it can cause problems. The increased percentage will inhibit the reaction of the ferrite compounds in the concrete and the surface will be darker.
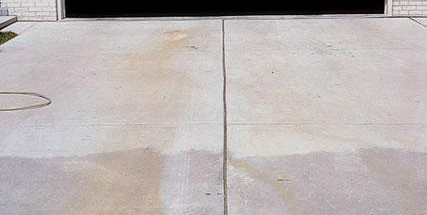
How can this discoloration be prevented? It is very important that all of the batches that come to the site are consistent in terms of the percentage of calcium chloride. Another consideration is that the percentage used should not exceed the amount as recommended in the ACI specifications.
This actual percentage of calcium chloride added and the consistent batching of the concrete have to be discussed at a preconstruction meeting. As with all of the causes of discoloration, this meeting is absolutely necessary in order to make sure that everyone involved; the materials provider, the mixing plant, and concrete flatwork company are all on the same page.
Finishing the surface
Burning the concrete
A concrete slab surface becomes “burnt” if, while finishing, the surface becomes too stiff to finish in a normal fashion. Because of this, the finishers have to vigorously trowel the surface to finish it. The vigorous troweling forces the water out of the surface layer which, reduces the water content in that portion of the slab and this causes the surface to darken. The more vigorous and extended the troweling, the darker the surface becomes. This process can result in the concrete being quite dark, sometimes even bordering on being black in color.
Metal trowel blades
Another factor that can cause this discoloration is the use of metal blades on the ride on trowels used for finishing. When the surface is troweled with metal blades, the abrading of the metal from the blades onto the surface does have a tendency to darken the surface.
The preventive measure for each of these problems is having language in the specification to state that the concrete finishers should use plastic blades on their power trowel and not burn or overwork the concrete surface.
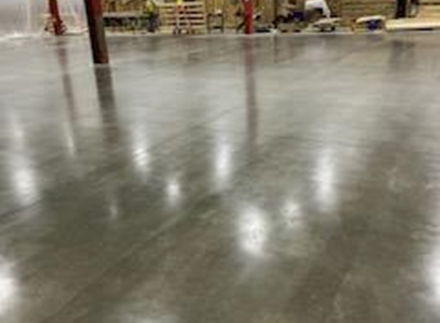
Inadequate, inappropriate, or lack of curing
The American Concrete Institute defines curing as; “the process of maintaining satisfactory temperature and moisture conditions in concrete long enough for hydration to develop the desired concrete properties. The potential strength and durability of concrete will be fully developed only if concrete is properly cured.”3
Quite often a covering material is used to cure a concrete slab. This is a very effective method! Problems occur when the covering is placed so the cover is not consistently in contact with the surface. If this is the case, the surface can appear mottled once the covers are removed.
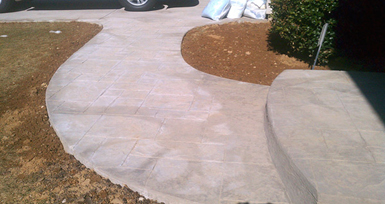
What happens is that there is a difference in how the water evaporates out of the surface of the concrete in the air pockets above the slab when the cover is not in direct contact. This causes differences in the cement-water ratio in that part of the slab. This causes light and dark mottling to appear on the surface. If this is repeated over all sections of the slab, this leads to a very mottled surface.
The way to avoid this problem is to make sure that the cover is in contact all over the slab, and remains so, for the entire curing process as per specifications.
Changes of raw materials in the concrete mix
Concrete is a very complex mixture. The type of cement, mineral admixtures, and sand can affect the color. Any variation in one of these components will cause a difference in color from one part of a floor to another. Any change in the concreting practices or even getting the same mixture from different plants can cause color problems.
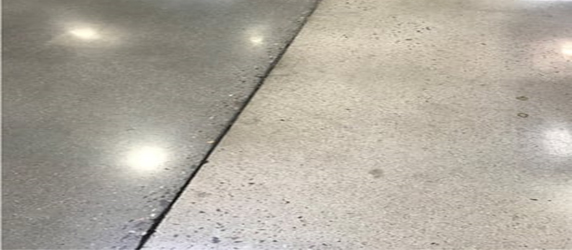
The picture above shows how drastic the difference can be from a change in the concrete delivered to a site. In order to avoid these problems, consistency is the key!
As a final remark, the Portland Cement Association (PCA) in an article on Surface Defects does a good job of summarizing how to avoid or minimize discoloration by: “(1) avoiding the use of calcium chloride admixtures, (2) using consistent concrete ingredients, uniformly proportioned from batch to batch, and (3) using proper and timely placing, finishing, and curing practices. Concreting practices should not be allowed to vary, as any disruption or change in the concrete mixture, formwork, finishing, or curing can result in significant and sometimes permanent discoloration.”2
Need Help With Your Concrete?
If you have any questions about the treatment, repair, or renovation of your concrete floor, give us a call at 716-831-7091 or email us at info@themjacompany.com.
1 ConcreteSouth
2 Portland Cement Association
3 American Concrete Institute
4 Concrete Decor & Professional Trade Publications Inc.
5 Bartell Global